- home
Stress and Sealing Mechanisms in Ferrule Fittings
Published on 3 October, 2024
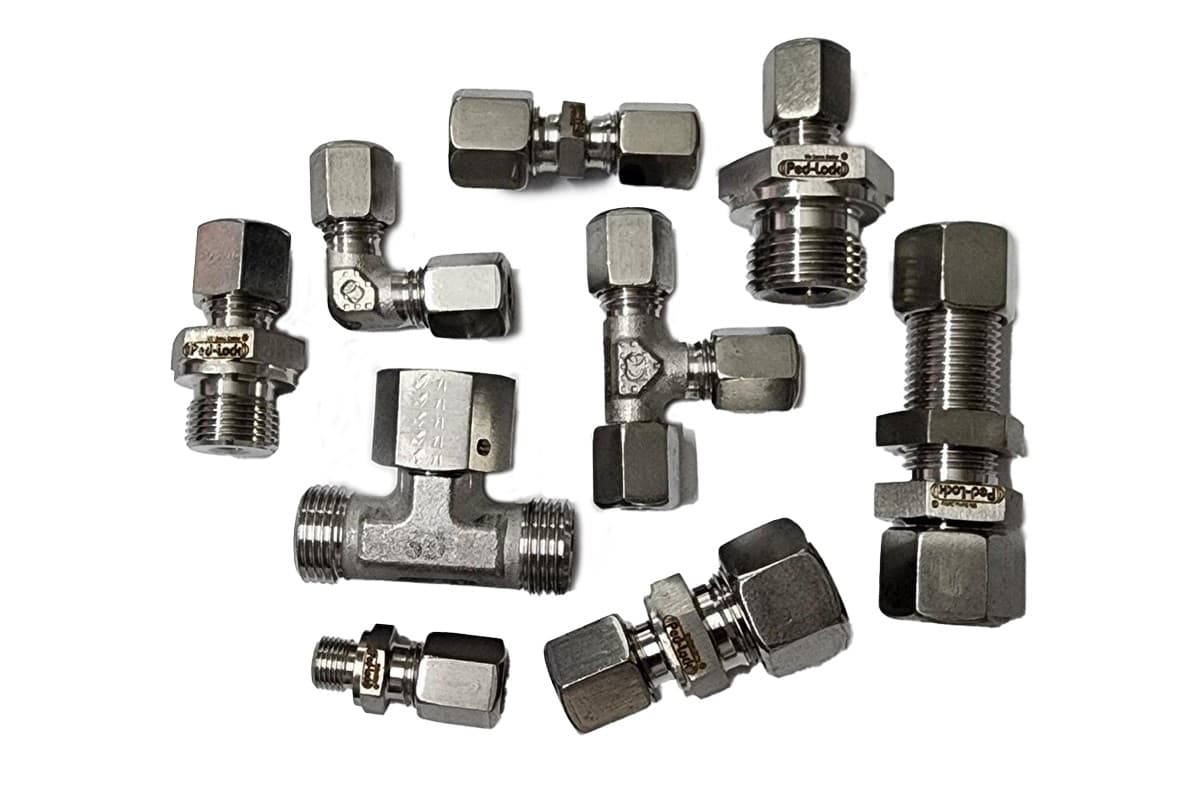
When it comes to industrial piping systems, ferrule fittings are essential in securing leak-proof connections, especially in high-pressure environments. These fittings are widely used in sectors like chemical processing, oil and gas, and instrumentation. If your business deals with supplying or installing industrial-grade piping, understanding the stress and sealing mechanisms in ferrule fittings can help heighten performance and avoid costly failures.
What Are Ferrule Fittings?
Ferrule fittings are a type of compression fitting that ensures a secure, leak-proof connection by compressing a small ring (ferrule) against the tube and the fitting body. The fittings are often made from materials like stainless steel, brass, copper, or other metals that provide the necessary strength and corrosion resistance.
Stress in Ferrule Fittings
Ferrule fittings experience three primary types of stress: Axial, Hoop, and Radial:
1. Axial Stress: Keeps tubing stable under internal pressure. In gas pipelines, it prevents longitudinal distortion and secures leak-proof connections.
2. Hoop Stress: Acts around the tube’s circumference to maintain structural integrity. For instance, in high-pressure water filtration systems, hoop stress prevents pipe collapse.
3. Radial Stress: Compresses the ferrule into the tubing, ensuring a tight seal. This is vital in fuel systems, where radial stress maintains leak-proof connections even in high-vibration environments.
Stress Relaxation
Over time, due to constant exposure to pressure and temperature changes, ferrule fittings may experience stress relaxation and a gradual reduction in the stress applied. For businesses in industries like oil and gas, where high temperatures are common, choosing materials like Monel 400 helps mitigate stress relaxation due to its excellent thermal stability, providing long-term sealing performance.
Sealing Mechanisms in Ferrule Fittings
Ferrule fittings create a metal-to-metal seal through radial compression. A double ferrule design not only improve sealing but also increases mechanical grip on the tubing, preventing slippage in high-vibration environments. In the pharmaceutical industry, where sterility and precision are critical, double ferrule fittings guarantee that connections remain secure under fluctuating pressures and temperatures.
For example, the front ferrule provides a tight seal, while the back ferrule grips the tube, making sure both structural integrity and the ability to handle high-pressure flow without deformation. This design also reduces the risk of over-tightening, which can damage delicate tubing in sensitive environments like labs and cleanrooms.
Material Selection for Ferrule Fittings
Below is a table comparing various materials commonly used in ferrule fittings and their ideal applications based on pressure, temperature, and corrosion resistance.
Material | Pressure Handling | Temperature Range | Corrosion Resistance | Ideal Applications |
Stainless Steel 316 | Up to 10,000 PSI | -200°C to 600°C | High | High-pressure hydraulic systems, chemical processing industries. |
Hastelloy C276 | Up to 6,000 PSI | -196°C to 400°C | Excellent | Corrosive environments, offshore oil platforms. |
Monel 400 | Up to 5,000 PSI | -240°C to 480°C | Very High | Corrosive environments, offshore oil platforms. |
Brass | Up to 3,000 PSI | -40°C to 200°C | Moderate | Low-pressure water systems, plumbing, and gas lines. |
Technical Standards for Ferrule Fittings
1. ASTM A276: Specifies the mechanical properties of stainless steel used in ferrule fittings.
2. ASME B31.3: Ensures piping systems in refineries and chemical plants meet safety and performance criteria.
3. ISO 8434-1: International standard for metallic tube fittings, ensuring compatibility and safety.
Choosing the Right Ferrule Fittings
1. Material Compatibility: Make sure the material of the fitting is compatible with the fluids or gases being transported to avoid chemical reactions that could damage the system.
2. Pressure Rating: Ensure the fitting can handle the system's operating pressure. Stainless Steel 316 is a popular choice for high-pressure hydraulic systems due to its strength.
3. Temperature Range: Some materials, like Monel 400, perform well under extreme temperature fluctuations, making them ideal for both cryogenic and high-temperature applications.
4. Fitting Configuration: See that the fitting’s size and design match the system's layout. Mismatched fittings can result in leaks and inefficient operation.
Whether you are providing high-pressure hydraulic systems or be in specialized environments like pharmaceutical production, our Guide to Essential Pharmaceutical Production Metal Fittings can help you choose the right materials and fittings for optimal performance.
At Online Fittings, we provide reliable, industry-compliant ferrule fittings that warranty performance and safety in even the most demanding environments. Contact us to explore our range of fittings and find the best solutions for your business.
Recommended blogs
For Further Inquiry

+91 9004790045
Online Fittings is a privately held stockiest and distributors of Stainless Steel and Alloy Steel, the head office in Mumbai.Our company's vision is to understand our customers requirements and meet them fully to their entire satisfaction by way of high quality, competitive price and prompt service.