- home
Forged Fittings v/s Cast Fittings: Key Differences in Tensile Strength
Published on 15 October, 2024
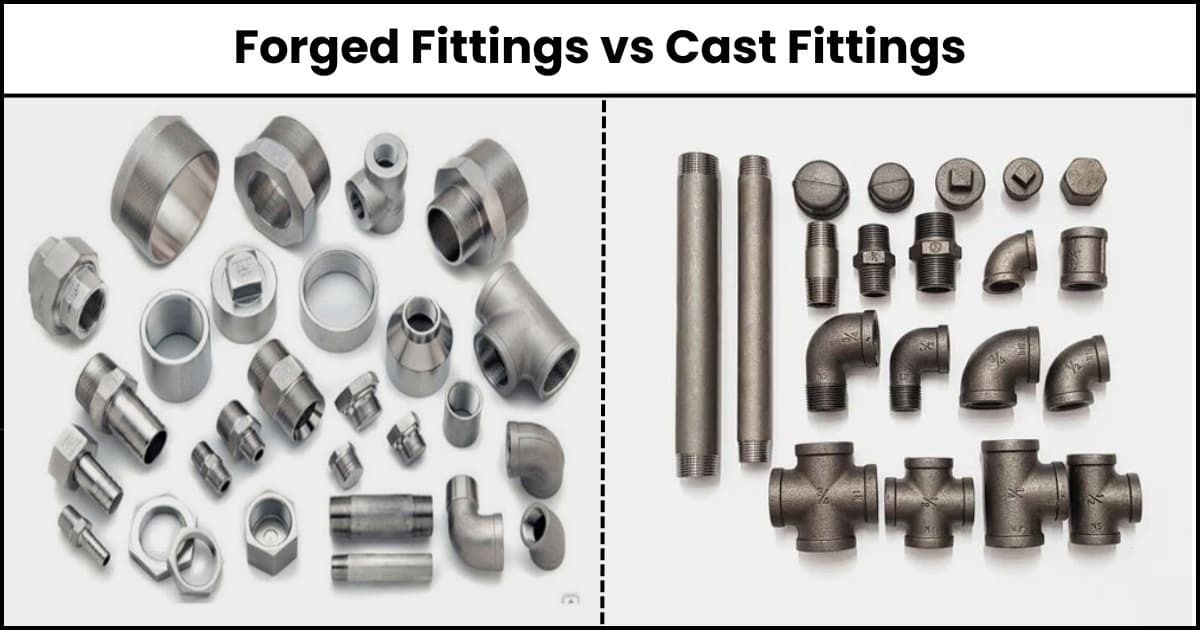
Imagine your customers are relying on you to provide the fittings that will keep their high-pressure systems running flawlessly. Whether it’s a refinery or a chemical plant, the products you deliver must endure extreme stress. The choice between forged and cast fittings is not just about how they are made; it’s about ensuring they have the tensile strength to handle demanding conditions. Understanding the key differences between these two types of fittings is essential for the durability of your products and your customers’ satisfaction.
Understanding Forged Fittings
Forged fittings are created through a manufacturing process known as forging, which involves heating the metal and then using mechanical forces (hammering or pressing) to shape it. This process alters the internal structure of the metal, creating a stronger and more durable product.
Manufacturing Process
1. Forging Temperature: Typically ranges from 900°C to 1250°C.
2. Materials Used: Commonly made from carbon steel (A105), alloy steel (F11, F22), or stainless steel (SS316, SS304).
3. ASTM Standards: Forged fittings often comply with ASTM A182 (for stainless and alloy steel) and ASTM A105 (for carbon steel).
Tensile Strength
Tensile strength refers to the maximum stress a material can withstand while being stretched or pulled before breaking. Forged fittings tend to have superior tensile strength due to the grain flow patterns created during the forging process. These grain flows align in a way that increases resistance to tensile forces, making forged fittings more robust under high-pressure conditions.
Typical Tensile Strength:
1. Carbon Steel (A105): 485 MPa (min)
2. Alloy Steel (F22): 620 MPa (min)
3. Stainless Steel (SS316): 515 MPa (min)
Forged fittings are known for their uniform structure, offering higher resistance to mechanical stress, ideal for high-pressure applications in oil and gas, chemical processing, and industrial pipelines.
Understanding Cast Fittings
Cast fittings are produced by pouring molten metal into a mold and allowing it to cool and solidify into the desired shape. The casting process allows for intricate designs but can introduce small imperfections, such as porosity, which can affect the overall strength.
Manufacturing Process
1. Casting Temperature: Dependent on the material used; steel casting is typically performed around 1535°C.
2. Materials Used: Cast fittings are often made from grey cast iron, ductile iron, or cast steel.
3. ASTM Standards: These fittings often meet ASTM A216 (for carbon steel castings) or ASTM A351 (for stainless steel castings).
Tensile Strength
Compared to forged fittings, cast fittings generally exhibit lower tensile strength. The cooling process can lead to voids or porosity, reducing the material's ability to withstand tensile forces. However, cast fittings are often used in applications where pressure and tensile loads are lower, or where complex shapes are required.
Typical Tensile Strength:
1. Cast Steel: 485 MPa (min)
2. Grey Cast Iron: 200 MPa (min)
3. Ductile Iron: 414 MPa (min)
While cast fittings are easier to produce in complex shapes, they are often less resistant to high-stress conditions due to the lack of grain alignment found in forged fittings.
Forged fittings are clearly superior when it comes to tensile strength, making them ideal for applications where fittings need to withstand significant stress and pressure, such as in petrochemical plants, refineries, and power generation.
Why Tensile Strength Matters for Buyers
When choosing between forged and cast fittings, buyers must consider the specific demands of their application. The higher tensile strength of forged fittings means they are less likely to fail under stress, ensuring longer service life and reducing the risk of costly failures. Cast fittings, while lower in tensile strength, may be more appropriate for low-pressure applications or where complex shapes are needed.
Industrial Standards to Consider:
1. ANSI/ASME B16.11: Standard for forged steel fittings, covering pressure and temperature ratings.
2. ASTM A182: Specification for forged stainless steel piping components.
3. ASTM A216/A351: Standards for carbon and stainless steel castings, respectively.
Choose Your Metal Wisely: Applications
As industries evolve, the demand for high-quality materials in construction and architecture grows. Just as tensile strength matters in fittings, material choices like stainless steel, copper have become equally important in design and durability. If you are interested in how material strength influences design choices, explore our blog on the Benefits of Copper in Modern Architecture, and discover how our raw materials can boost your business offerings.
At Online Fittings, we offer a wide range of forged and cast fittings that adhere to extreme industrial standards, making sure the highest quality for your industrial needs. Contact us today to ensure your customers receive the best materials for their toughest projects.
Recommended blogs
For Further Inquiry

+91 9004790045
Online Fittings is a privately held stockiest and distributors of Stainless Steel and Alloy Steel, the head office in Mumbai.Our company's vision is to understand our customers requirements and meet them fully to their entire satisfaction by way of high quality, competitive price and prompt service.