- home
The Backbone of Modern Connectivity: What Goes into Setting Up a Strong Bridge Structure?
Published on 28 April, 2025
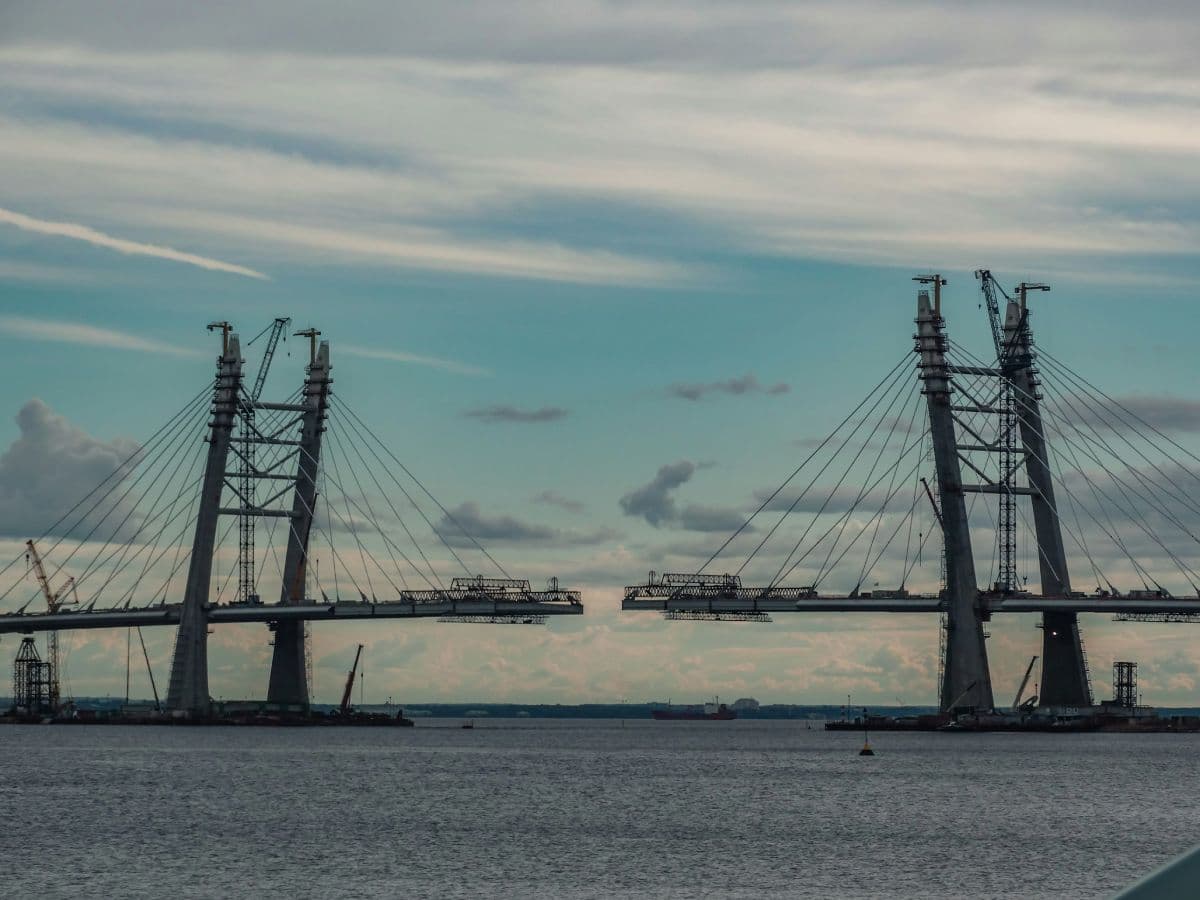
As the morning horizon unfurls, bridges ascend above water and valley alike, sovereign sentinels that fortify economies, orchestrate human movement, and symbolise our collective engineering ethos. Take the Mumbai Trans Harbour Link, which connects Mumbai and Navi Mumbai in a matter of minutes and requires about 96,250 tonnes of structural steel for its 21.8 km of spans. Across low‑income regions, simple footbridges and paths dissolve barriers for nearly one billion rural inhabitants, granting safe passage to schools, clinics, and marketplaces.
Foundations of Modern Bridge Engineering
1. Material Selection
a. Structural Steel: The ASTM A709 specification, which offers grades from A709 36 to high-performance steels like HPS 70W with enhanced atmospheric corrosion resistance indices greater than 6.0, specifies the chemical and mechanical requirements for bridge-grade structural steel. Chemical composition is verified through heat analysis to control alloying elements (C, Mn, P, S, Si, Cu), while tension tests ensure that yield strengths (e.g., 345 MPa for Grade 50). In harsh conditions, weathering grades (50W, HPS 50W, and HPS 70W) develop protective patinas that reduce maintenance.
b. High‑Performance and Ultra‑High‑Performance Concrete: Advanced concrete mixtures incorporate supplementary cementitious materials (silica fume, fly ash) and superplasticisers to achieve compressive strengths exceeding 100 MPa with low permeability. Ultra‑High‑Performance Concrete (UHPC) formulations, reinforced with quartz powder and steel fibers, deliver compressive strengths above 150 MPa and superior durability, enabling thinner deck overlays and extended service lives beyond 75 years. Controlled curing regimes and admixture optimisation are critical for microstructure densification and crack mitigation.
2. Foundation and Substructure
a. Geotechnical Investigations: Comprehensive subsurface exploration such as borings, Standard Penetration Tests (SPT), Cone Penetration Tests (CPT), and laboratory soil characterisation, establishes bearing capacities, settlement potentials, and liquefaction risks. Geological mapping detects bedrock depth, while geophysical surveys (seismic refraction) can delineate subsurface anomalies. Data informs foundation type selection and scour countermeasures.
b. Deep Foundations and Scour Protection: Designers choose between driven piles (steel H‑piles, pipe piles) and bored shafts (drilled caissons) based on soil stratigraphy, load demands, and environmental constraints. Pile capacities are calculated via axial and lateral load tests, with factor‑of‑safety margins by AASHTO LRFD guidelines. Scour protection like riprap, articulated concrete mats, or grout‑filled bags is dimensioned to resist high‑velocity flows and prevent undermining of piers.
3. Erection and Construction Techniques
a. Launching Gantry and Incremental Launching: A launching gantry supports span‑by‑span erection, moving complete segments forward on temporary bearings as prestressing occurs in situ. Alternatively, incremental launching pushes the entire superstructure from one abutment using sliding bearings and hydraulic jacks, ideal for minimal access sites. Both techniques demand precise surveying and load monitoring to maintain alignment and stress limits.
b. Welding, Bolting, and Quality Control: High‑strength bolts (ASTM A325/A490) and full‑penetration welding procedures ensure moment continuity in steel connections. Non‑destructive tests (ultrasonic, magnetic particle) validate weld integrity. Dimensional tolerances are verified against shop drawings, while concrete components undergo cylinder break tests and rebound hammer surveys for compressive strength assessment.
4. Durability, Corrosion Protection, and Maintenance
a. Coating and Galvanising: Hot‑dip galvanising imparts barrier and sacrificial protection, achieving zinc layer thicknesses of 85–185 µm for 100‑year design lives in atmospheric exposure. Organic coatings, epoxy primers with polyurethane topcoats offer aesthetic flexibility and additional barrier performance.
b. Cathodic Protection Systems: Galvanic cathodic protection employs zinc anodes or impressed‑current systems to shift steel to cathodic potentials, reducing corrosion rates from ~1% to 0.04% per year in marine environments. Under harsh conditions, zinc mesh jackets around pilings have been shown to increase service lifetimes by decades.
Why buy Steel from Online Fittings?
As a leading online supplier of industry raw materials, Online Fittings assures project teams have the critical materials to meet today’s connectivity challenges with future‑proof reliability. Contact us to discuss customised supply solutions for your next bridge project.
Recommended blogs
For Further Inquiry

+91 9004790045
Online Fittings is a privately held stockiest and distributors of Stainless Steel and Alloy Steel, the head office in Mumbai.Our company's vision is to understand our customers requirements and meet them fully to their entire satisfaction by way of high quality, competitive price and prompt service.