- home
Ferrule Fittings for Chemical Plants: How to Prevent Corrosion and Wear
Published on 26 November, 2024
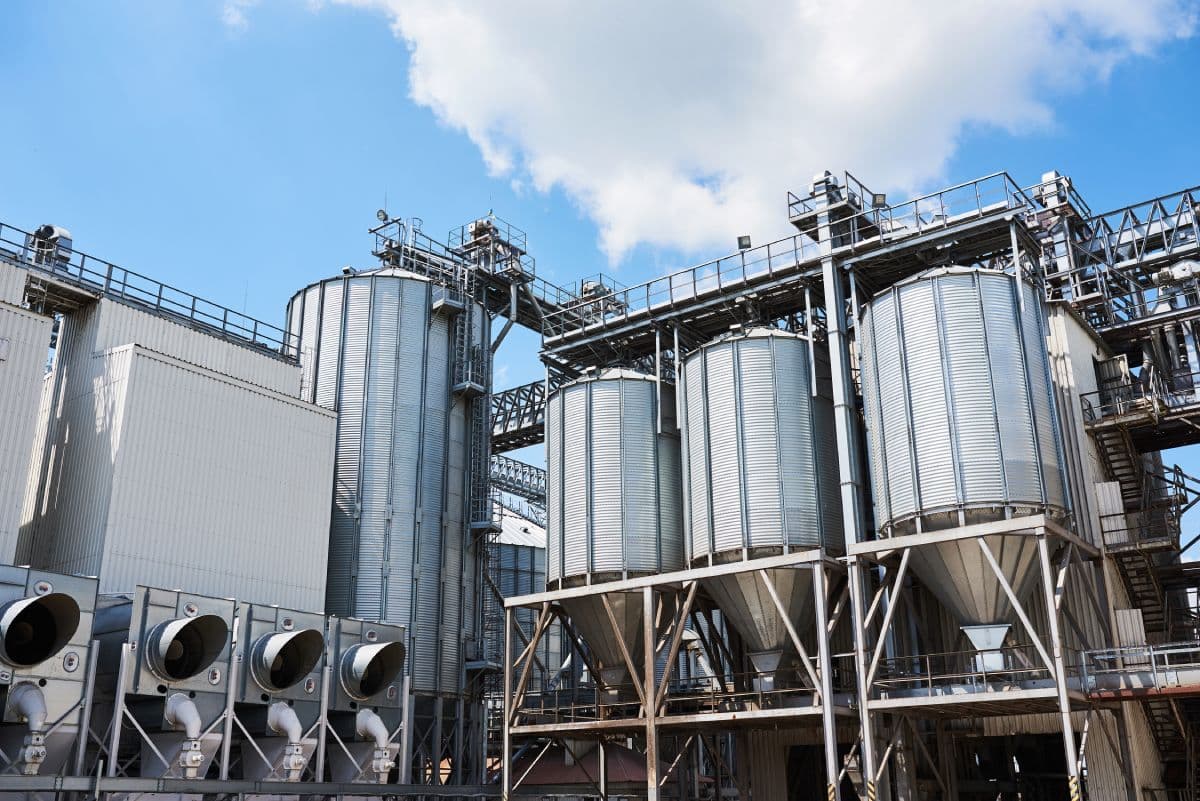
In chemical plants, where aggressive substances and extreme conditions are the norm, every component in a piping system must meet the highest technical and material standards. Among these components, ferrule fittings play a crucial role in maintaining safe and leak-proof operations. However, the harsh environments in these plants make ferrule fittings prone to corrosion and wear, potentially disrupting the system's efficiency and safety.
What Are Ferrule Fittings?
Ferrule fittings are mechanical connectors that create a secure seal in piping systems, even under high pressures and temperatures. They are composed of:
1. Body: The main structure that guides fluid or gas.
2. Nuts: Tightens the assembly by compressing the ferrule.
3. Single or Double Ferrule: The key sealing element that grips the pipe or tubing tightly.
Key technical features of ferrule fittings include:
1. Pressure Ratings: Typically ranging from 3000 psi to 10,000 psi, based on material and size.
2. Temperature Tolerance: Withstands up to 1000°F (538°C) in materials like Inconel.
3. Threading Standards: Commonly follows NPT (National Pipe Thread) or ISO Metric Threads.
For chemical plants, double-ferrule fittings are widely preferred due to their superior stress distribution and sealing capabilities in challenging conditions.
Understanding the Threats For Corrosion and Wear for Ferrule Fittings
Ferrule fittings in chemical plants face a range of operational challenges:
1. Chemical Corrosion: Caused by exposure to acids (like HCl, H₂SO₄) and alkalis present in fluids.
2. Galvanic Corrosion: Occurs when dissimilar metals come into contact, especially in saline environments.
3. Fretting Wear: Results from micro-movements in vibrating systems, leading to gradual surface damage.
These challenges, if not addressed, can result in material failure and compromise safety and efficiency across the system.
Effective Strategies to Combat Corrosion and Wear for Ferrule Fittings
Surface Treatments and Coatings
1. Electropolishing: Smoothens surfaces, reducing impurities that trigger corrosion.
2. PTFE Coatings: Chemically inert and shields against reactions with aggressive substances.
3. Nickel Plating: Adds a protective surface layer, especially in oxidising environments.
Gaskets and Liners
Adding PTFE or elastomeric gaskets can separate dissimilar metals, preventing galvanic corrosion.
Optimised Design Features
1. Double Ferrule Fittings: Provide even stress distribution to minimise deformation.
2. Anti-Vibration Clamps: Reduce wear caused by system vibrations.
Maintenance and Testing
1. Hydrostatic Testing: Periodic pressure tests detect potential weak points.
2. Spectrographic Analysis: Monitors chemical composition to identify early signs of degradation.
3. Regular Cleaning Protocols: Non-abrasive cleaners extend the lifespan of the fittings.
Advanced Material Grades for Ferrule Fittings
Material Grade | Technical Properties | Applications |
316Ti Stainless Steel | Provides resistance to intergranular corrosion due to titanium stabilization. | Suitable for systems handling hot organic and inorganic chemicals. |
Inconel 625 (UNS N06625) | Offers outstanding resistance to chloride-induced stress corrosion cracking and oxidation. | Used in high-chloride and oxidizing environments. |
Hastelloy C22 (UNS N06022) | Resists both oxidizing and reducing agents and is known for its excellent weldability. | Ideal for multi-reactant systems in chemical plants. |
Duplex Stainless Steel 2205 | Balances high strength with resistance to pitting and crevice corrosion. | Best suited for sulfur-rich environments. |
Titanium Grade 2 | Lightweight with excellent corrosion resistance in acidic and saline conditions. | Frequently used in heat exchangers and reactors. |
For example, Inconel 625 is often chosen for systems transporting chloride-heavy brines, while Hastelloy C22 performs exceptionally in chemical reactors involving mixed acid environments.
Standards and Certifications for Ferrule Fittings
Compliance with industry standards assures the reliability and performance of ferrule fittings. Some key standards include:
1. ASME B16.11: Covers forged fittings for high-pressure applications.
2. NACE MR0175/ISO 15156: Specifies materials for hydrogen sulfide (H₂S)-rich conditions.
3. ISO 8434-1: Defines compression fitting design, dimensions, and performance.
4. ASTM A479/A182: Specifies stainless steel bars and forgings for high-temperature service.
5. DIN 3852: A German standard for leak-proof connectors and pipe fittings. .
Ferrule fittings are a cornerstone of safe and efficient chemical plant operations, where their ability to manage stress and sealing mechanisms is vital to countering the challenges of corrosion and wear. We specialize in providing high-performance ferrule fittings tailored to the demanding requirements of chemical plants. Explore our extensive product range and take the first step toward safer, more durable operations.
Contact Online Fittings today to discuss how we can support your specific needs and ensure your systems perform at their peak!
Recommended blogs
For Further Inquiry

+91 9004790045
Online Fittings is a privately held stockiest and distributors of Stainless Steel and Alloy Steel, the head office in Mumbai.Our company's vision is to understand our customers requirements and meet them fully to their entire satisfaction by way of high quality, competitive price and prompt service.